勇闯技术“无人区” 白鹤滩水电站建设科技攻关成果丰硕
今日热点:
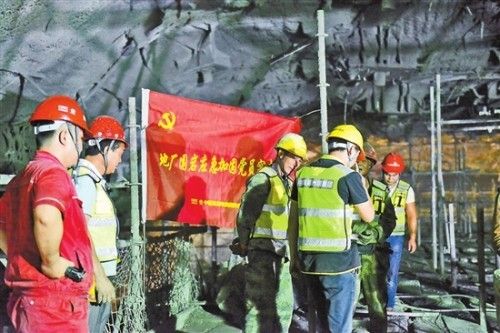
令世界瞩目的白鹤滩水电站,在建设过程中,创下水轮发电机容量、地下硐室群规模、圆筒式尾水调压室规模、300米级高拱坝抗震参数、无压泄洪洞群规模、首次全坝使用低热水泥混凝土等6项世界第一,“每一项世界第一,就意味着要解决一系列世界性难题。”三峡集团副总经理范夏夏说,世界首次全坝使用低热水泥混凝土浇筑,以及智能建造技术的应用,白鹤滩工程建设就这么闯过一项项技术“无人区”,最终建成世界第一座无裂缝大坝。
![]() |
世界首座无缝大坝
5月31日12时07分,弧长709米的白鹤滩水电站拱坝坝顶完美地呈现在金沙江上,也标志着我国300米级特高拱坝建造技术实现突破。白鹤滩水电站大坝建设创造了年浇筑270万立方米、月浇筑27.3万立方米、百日过深孔等同类工程的世界纪录,大坝主体混凝土浇筑总量达803万立方米,“体积”超过3个胡夫金字塔。“大坝没有产生过一条温度裂缝,标志着我国已完全掌握大体积混凝土温控防裂关键技术。”三峡集团白鹤滩工程建设部主任汪志林介绍,白鹤滩水电站仅在大坝建设中,就攻克了柱状节理玄武岩作为特高拱坝坝基的世界级难题,创新实施百米门槽一期直埋等领先技术,推动了行业技术进步。
一直以来,白鹤滩水电站工程秉承“全面推行标准化工艺,全面创建精品工程,全面防控质量风险”的质量管理方针,严控大坝混凝土备仓和浇筑质量,实行大坝项目部监理、承包人三级管理人员24小时联合值班制度。“我们组织参建各方系统梳理各项准备工作,编制大坝混凝土开浇前准备工作导则,提出了大坝浇筑‘仓仓精品’的目标。”白鹤滩大坝项目部工程师刘春风介绍,“仓仓精品”意味着大坝备仓浇筑的每一个环节都需要高标准施工和严格管控,为保证浇筑工艺稳定、备仓有序高效,混凝土标准化工艺应运而生。“比如在廊道周边混凝土人工振捣的操作环节,混凝土要振捣几遍,振捣棒型号如何选择,初振的振捣时间是多长,复振的时间是多长,初振与复振的间隔时间有多长等等这些参数均依据专业试验得出,再把这些参数纳入标准化工艺手册中,用于员工培训,指导施工。”
白鹤滩水电站大坝在世界上首次全坝采用低热水泥混凝土进行浇筑,低热水泥混凝土温控技术没有成熟的经验可以借鉴。建设者们始终保持创新、探索的精神,在大坝开浇前制定了《拱坝混凝土温控施工技术要求》的试验本。三峡集团白鹤滩工程建设部和参建各方开展“智能大坝”技术的研究和运用,浇筑一条龙智能监控、智能通水、智能灌浆等智能技术,为建成无缝大坝及保障大坝长期安全稳定运行提供了创新解决方案。“我们运用智能大坝的相关技术,实现精细化温控管理,有效避免了温度裂缝的产生,保证工程质量。”工程建设部大坝项目部工程师谭尧升告诉记者,大坝中埋设的5774支温度计、75347米的测温光纤、数千支监测仪器,用于感知气温、风速、温度应力、应变等信息,可以实现混凝土生产、运输、浇筑、运行的全生命周期监控,对施工进度、质量进行可视化分析。
多层“蛋糕”里造“心室”
大坝两侧的地下深处,洞室纵横交错,宛若一个巨大的地下迷宫。这里是16台百万千瓦机组的“栖息之地”——白鹤滩水电站地下厂房,其洞室群规模、厂房跨度、调压室直径和数量均居世界水电工程之首。与“世界之首”的美誉相伴而来的,是技术、管理方方面面难题和一个个待攻破的“无人区”。白鹤滩水电站地下厂房的设计、施工与管理,某种程度超越了现有规范和已有工程经验。面对挑战,白鹤滩工程建设者勇攀科技高峰,勇闯“无人区”,通过不断创新,攻克一个个难关,打造出一座恢弘精细的“地下城”。
白鹤滩水电站地下厂房洞室群规模世界第一,结构布置复杂,埋深大,地下洞室开挖量2500万方,开挖总里程约230千米。记者探访的右岸地下厂房位于坝肩上游山体“腹内”,厂房面积有2个足球场大,高约30层楼高。最大水平埋深800米,最大垂直埋深540米。
“白鹤滩水电站地处深V型峡谷,两岸空间有限,需要开挖地下洞室,布置引水发电系统设备。”具体负责白鹤滩右岸地下厂房施工建设的中国能建葛洲坝三峡建设公司白鹤滩施工局常务副局长王林告诉记者,与地上建房不同,地下厂房开挖从“天花板”开始,一层一层往下开凿。事实上,高边墙围岩变形与稳定,一直是大型地下洞室开挖中的一项世界性难题。而白鹤滩水电站地下厂房位于横断山脉,处于川滇地震带上,岩石层与层之间柱状节理明显、裂缝极多,更使得围岩变形与稳定难上加难。
“右岸地下厂房不仅开挖断面尺寸大、埋深大,还穿越3条大的不良地质发育带和近50条层间错动带,地应力极高。”王林形容道,开挖右岸地下厂房,就好比在松软多层的“蛋糕”中挖一个又深又大的洞,不仅要根据对围岩岩性的不断认知调整施工方法,还要应对地下洞室挖空率不断变大、应力调整带来的高边墙变形,施工难度可想而知。经过反复研究和摸索,葛洲坝集团白鹤滩施工局现场创新采用“小梯段、短循环、弱爆破、强支护”的施工方法,同时革新了爆破控制技术,有效控制了围岩边墙的深层变形,将变形量控制在0.5毫米的范围内。为了加固围岩,施工人员还像穿针引线纳鞋底般,在整个厂房岩石上施行9460束锚索,比同规模电站多出一倍。如今,行走在右岸地下厂房,已看不到锚索的痕迹。早在2018年7月,厂房就转入混凝土施工阶段,最高峰时创造了单班3000方混凝土的浇筑纪录。厂房板梁柱墙全部采用免装修混凝土施工新工艺,光滑平整可鉴。
为提高混凝土施工效率,白鹤滩工程建设部在施工设备创新上也下足了功夫。为减少钢模台车的拆装次数,加快施工进度,规避人工拆装台车的安全风险等问题,研发出一种可横向移动的伸缩式钢模台车,能够平移至相邻隧洞,大大节约台车安拆工期。在白鹤滩右岸地下厂房的施工现场,记者见识这一施工“神器”,据与制造企业联手开发这种“伸缩台车”的葛洲坝集团白鹤滩施工局总工程师邓富扬介绍,该项设备的研发使用,进一步减少了人工投入,提高了工效,保证了施工质量,实现了以科技创新手段促进经济效益提升的目的。
世界性难题成为过去时
在大坝左岸的地下洞室里,藏着三条名为泄洪洞的水工建筑物。作为世界级水电工程,白鹤滩水电站泄洪洞具有大泄量(每秒12250立方米)、大断面(15米×18米)、大坡度(最大23°)、高流速(最大每秒47米)、高水头(189米)、高强度(混凝土强度),每一项都是世界级难题。白鹤滩建设者坚持创新引领,用“体型精准、平整光滑、耐磨防裂、零缺陷”的精品混凝土质量回应挑战,施工采用智能温控解码关键点,攻克大断面衬砌混凝土“无衬不裂”世界性难题,实现衬砌零温度裂缝;首次实现高流速流道全过流面浇筑低坍落度混凝土,填补国内外的技术空白;创建水工隧洞镜面混凝土施工成套工法及管理体系,彻底解决衬砌混凝土质量顽疾。
全面精品工程是白鹤滩水电站的建设目标,泄洪洞施工团队在项目初期就提出“体型精准、平整光滑、耐磨防裂、零缺陷”的目标,但是所有人都明白,这不是轻而易举就能实现的。“泄洪洞流道较长,在高速水流作用下,对其抗冲磨、防空蚀性能要求极高。”白鹤滩水电站泄洪洞项目负责人王孝海告诉记者,混凝土缺陷修补费用高,施工缝面缺陷修补后,在高速水流下基本全部破坏,只有确保混凝土无缺陷才是保证运行期安全的基础。在泄洪洞混凝土施工过程中,施工团队科学定量地布置光纤测温仪器,精密的仪器就好比混凝土的神经末梢,能准确感知温度,为优化调整温控提供依据。有了神经末梢,当然还要赋予混凝土一颗聪明的“大脑”。找到了症结,就能对症下药,泄洪洞施工团队很快便锁定了温控的这一剂“良药”——智能温控。
在智能温控的帮助下,白鹤滩水电站泄洪洞实现了施工期零温度裂缝,智能方案的成功运用也让大断面衬砌混凝土“无衬不裂”这一世界性难题从此成为过去时。
高流速泄洪洞全过流面浇筑常态混凝土一直是国内水电行业从业人员的梦想。“就是因为常态混凝土有这么多的优点,国内有很多类似的工程在这方面进行了探索,但受限于洞室空间相对封闭、结构体型复杂、常规设备难以利用等问题,相关探索一直止步不前,没能真正实现。”王孝海介绍,泄洪洞龙落尾段边墙施工复杂、坡度大,想要实现常态混凝土可谓难上加难,“但为了实现精品工程的高标准,常态混凝土无疑是最好的选择。”王孝海说,在攻坚克难的关键时候,洪洞施工团队中的党员率先站了出来,对大坡度环境下常态混凝土运输展开专题研究,自主设计研发了大坡度重载自动化运料系统。“有了这套系统,我们只需要按下一个按钮就能将装有常态混凝土的运料小车从下料平台运往钢模台车。”作业人员对记者说,“这套系统实现了一键启动、全程自动控制,并配备四套安全控制装置,保证了常态混凝土运输效率和质量,也确保了运输过程的安全。”
2018年11月底,龙落尾边墙浇筑正式启动,距离全过流面浇筑常态混凝土只剩最后一块硬骨头——龙落尾底板浇筑,标志着水电行业一直以来未能在高流速泄洪洞全过流面浇筑常态混凝土的遗憾不复存在,填补了世界水电建设的技术空白。应用情况表明,白鹤滩水电站泄洪洞项目自行研制的成套常态混凝土施工装备安全、高效,较常规施工效率提高约20%。(云南日报 记者李继洪)
